Обработку разных поверхностей, как правило, производят путем использования пескоструйных устройств. Работа их осуществляется на основе сжатого воздуха, соответственно, при планировании их применения следует учитывать выбор некоторых параметров, важных для работ на пескоструе.
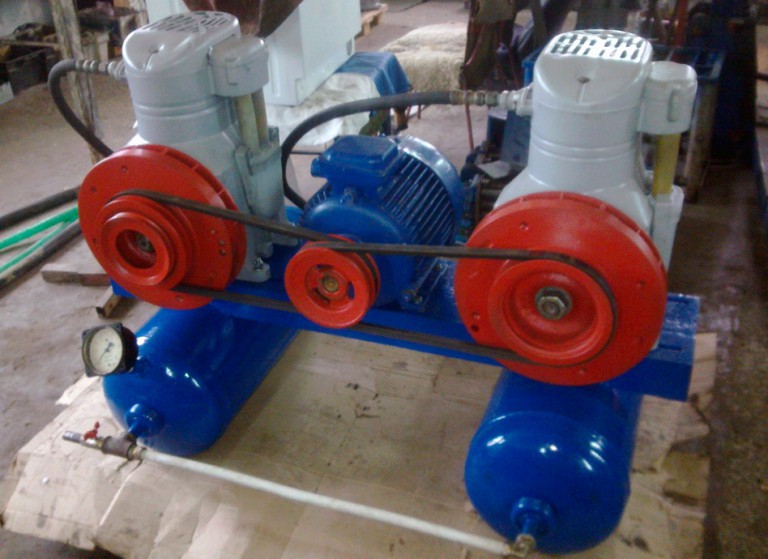
Всеми новейшими разработками по защите от коррозийных процессов используется сжатый воздух. Именно он служит основным источником энергии, своего рода движущей силой при работе по очистке и нанесении защитного состава. Данная статья предусмотрена, прежде всего, для тех, кто лишь приступает к решению проблем с антикоррозионной защитой. Однако также можно предположить, что и люди опытные смогут почерпнуть в ней для себя что-либо полезное, относительно выбора компрессора для пескоструя.
Как подобрать компрессор для проведения пескоструйной работы?
Вначале выбор компрессорных аппаратов с целью антикоррозионной защиты кажется довольно простой задачей. Но на практике оказывается, что если подойти к решению данной проблемы более тщательно, то на поверхность всплывают некоторые нюансы, которые требуют особого внимания к себе. Необходимо их учитывать, дабы уровень эффективности выбранных компрессоров и устройства, к нему подключенного, был максимальным.
Предположим, необходимое оснащение, обеспечивающее обработку против коррозии, уже было подобрано. Также определен диаметр сопелного сечения, выбраны приборы для проведения покраски и абразив, осталось только выбрать подходящий компрессор.
Чтобы остановиться на правильном выборе, следует проконсультироваться с поставщиками абразивоструйного оснащения относительно требований к давлению при работе, максимальных затрат воздуха под ним. Давление зачастую измеряется в барах, а также в атмосферах, что в принципе идентично. Рассчитывается потребление воздуха в кубометрах за минуту или в литрах за секунду.
Выбирается оптимальное рабочее давление для пескоструя, исходя из абразивных материалов, а также допустимой максимальной величины давления в абразивоструйных агрегатах. Как правило, уровень рабочего давления варьируется в пределах от 8 до 10 бар. При этом нужно учитывать, что с ростом давления увеличивается рабочий темп и ускоряется процесс износа шлангов и абразивных сопел.
Немаловажным моментом принято считать правильное определение количества потребления воздуха при давлении. Потому как во время подачи на потребляющие конструкции – абразивный или покрасочный аппарат воздуха ниже требуемых значений, станет невозможным, во-первых, достигнуть необходимого давления для работы, во-вторых, как результат первого, пострадает рабочая скорость и уровень производительности. Наихудший вариант – осуществление каких-либо работ вообще сорвется.
Например, недостаточная степень производительности компрессора мешает достигать необходимые при работе 8 бар, вместо них выдавая 3-4 бара. В таком случае абразив, не достигнув достаточного показателя скорости для очищения поверхности, попросту будет просыпаться из сопла в дополнение к нулевому эффекту работы. Подбирая компрессор для проведения пескоструйных работ, важно помнить – потребление напрямую зависит как от результата сечения сопла, так и от его типа (к примеру, конфигурации длины сопла). Кроме того, значение имеет и применяемый абразив (размерные и весовые характеристики). В качестве эквивалента в этой таблице была использована абразивоструйная работа, которую провели путем применения песка с плотностью в 1600 кг на кубометр.
В случае если ваш поршневой компрессор вышел из строя, вы всегда сможете заказать ремонт на сайте http://promkompressor.com/publications/polomki-i-remont-porshnevyih-kompressorov.html
Следует отметить, что при определении давления работы для осуществления покраски путем безвоздушного распыления, можно использовать диаграмму, указываемую, как правило, в технической документации. Необходимое при покраске рабочее давление, зачастую, насчитывает 4-6 бар.
Из-за недостаточной подачи воздуха может понизиться скорость подаваемой краски от необходимой, а это негативно может сказаться на рабочей скорости, или же агрегатный насос окажется не в состоянии осуществлять транспортировку краски до сопла.
При расчете потребления сжатого воздуха нужно учитывать и другие потребители, в частности, защитные шлемы пескоструйщиков. На один шлем, в среднем, приходится расход порядка 0,5 кубометров за минуту.